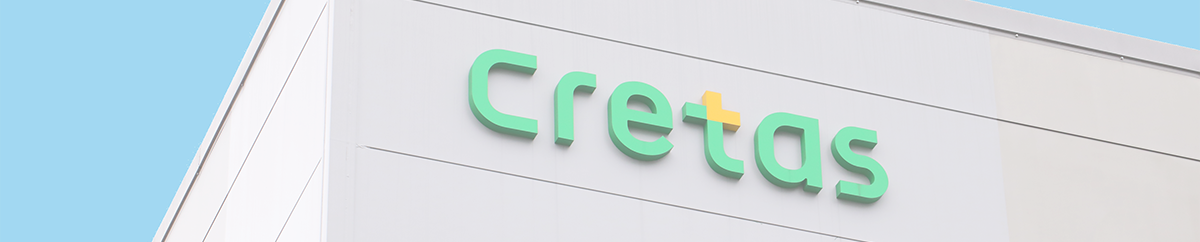
樹脂加工RESIN PROCESSING
試作用パーツの加工(3Dプリンター・注型)
どの加工方法にも一長一短があり、設計の各プロセスで上手な使い分けが必要となりますが、コストや納期を重視する場合は、今や3Dプリンターが一番最初に挙がるくらいには、メジャーな加工になるかと思います。
3Dプリンターとは、3D CADの設計データ(STLデータ)を元に、スライスされた二次元の層を1枚ずつ積み重ねていくことによって立体モデルを製作する機械のことです。
加工方式としては、主に『熱溶融積層法』、『光造形方式』、『粉末造形法』があります。
ここではそれぞれの加工方式と、それらを簡単に複製する『注型』についてのご紹介をしたいと思います。
◆熱溶解積層法
熱溶融方式の特許保護期間が2009年に終了したことで、様々な技術開発が進められ、今や一般的にもよく知られるようになりました。
基本的に『3Dプリンター』と言えば、この熱溶解積層法を思い浮かべる方も多いのではないでしょうか。
数万円で購入できる機種も販売されているので、個人所有する人も増え、データさえあれば複雑な形状も専門の加工業者に依頼せずに、簡単に製作することができるようになりました。
熱で樹脂を溶かして押し出しながら積層する方式で、熱可塑性の樹脂を使用できることが特徴です
樹脂の素材にもよりますが、耐久性や耐熱性もあるので試作品の製作に適していると言えます。
主にフィラメントと呼ばれる、紐状の材料を使う方式になります。
3Dプリンターのどの方式にも言える事ですが、素材を積層する方式になるため、表面に凹凸が生じてしまうデメリットがあり、滑らかな積層が必要な場合は向いていないとも言えます。
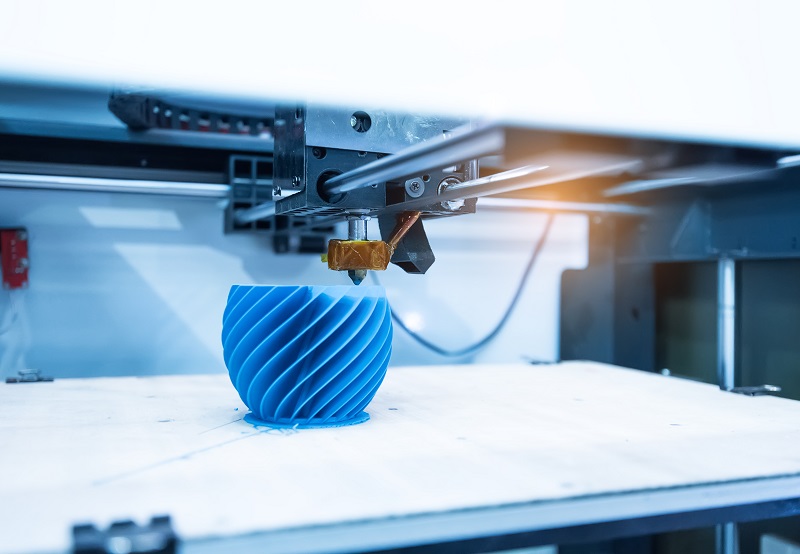
◆光造形
光硬化性の樹脂を満たしたプールに造形物が作られるテーブルを浸し、硬化させたい部分だけ光やレーザーを照射して、硬化させて部位を積層させて造形する方法です。
光やレーザーを上から照射するものと下から照射するもの、また光やレーザーを点で照射する方式と、面で照射する方式があります
現在、光造形方式の3Dプリンターでは、光やレーザーを下から照射するタイプが主流となっています。
他の方式と比較すると、滑らかな表面の再現や、複雑な形状の造形を高精度で実現することができる、といったメリットがあります。
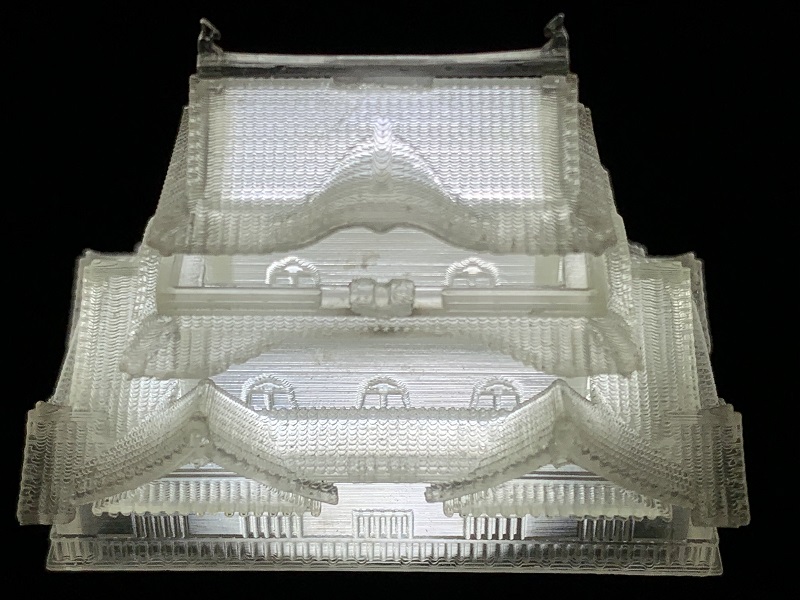
◆粉末造形(粉体造形)
粉末造形とは、粉末状の樹脂材料にレーザービームなどを照射することで焼結し、硬化させた部位を積層させて造形する方法です。
粉末状のナイロン樹脂やセラミック、金属など素材選択の自由度が高く、他の方式と比べて強度や耐久性も高いことから、ヒンジなどの突起形状を作成しても、ある程度は機能するといった特長があります。
また、これらの特長に加えて表面処理で面粗さを細かくすることもできるため、最終的な製品としての実用も進んでいる造形方式です。
※焼結:固体粉末の融点以下の温度で加熱することによって緻密な物体として固まる現象
◆注型
液状の材料と硬化剤を混ぜたものを型に流し込んで固めて作る加工方法です。
加圧や加熱が必要ないので、簡易的な型でスピーディーに複雑な形状を製作することが可能になります。
この加工方法に適合する材料はあまり種類がなく、エポキシ樹脂やポリウレタンなどです。
主に試作モデルの複製で用いられる加工方法になり、最終的には射出成形で量産するような製品を、試作段階で少数複製したい時などに使用します。
対象となるモデルの周りに液体状のシリコンを流し込み、固まったところで半分に切ってモデルを取り出すと、簡易的なシリコン型が出来上がります。
この型に材料を流し込んで固めることで、試作モデルと同じ形状のものを簡単に複製することができます。
軟らかいシリコン型で作りますので、金型を用いて作る射出成形より寸法の精度は落ちます。
また、一つの型で複製できる製品は数個~10数個程度で、それ以上作りたいという場合は、新たに型を作るところからやり直さなければならないといったデメリットがあります。