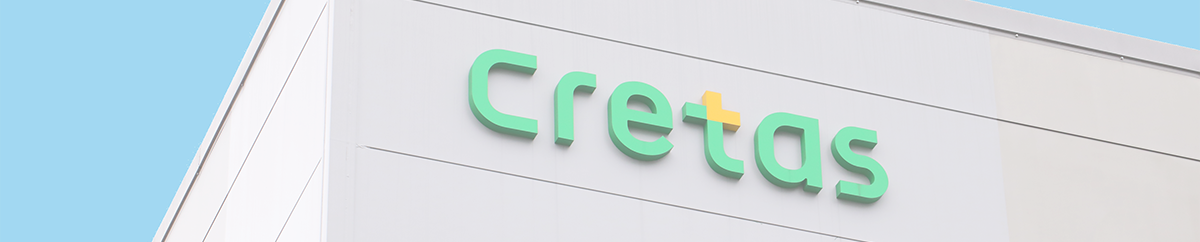
樹脂加工RESIN PROCESSING
シート成形(真空成形・圧空成形)
◆シート成形とは
熱可塑性樹脂は加熱すると軟化して形を変えることができ、冷やすと硬化するという特徴があります。
一度硬化した材料でも、再加熱すれば軟化して繰り返し変形させることができます。
この特性を活かし、シート(プラスチック板)を加熱して軟化させ、型にシートを押し付けたり、シートに型を押し付けたりして型の形状を写し取って成形することをシート成形と呼びます。
成形後に必ずトリミングをする二次加工工程があるので、穴位置が違う部品や切欠きのある部品など、類似形状の多品種で同じ金型を使用して製作できる場合もあります。
ペレットを融解させて成型する射出成形などと異なり、数枚~20枚程度の少量から製作することができます。
金型の形状を、シートにどうやって写し取るかによって、いくつかの加工方法があります。
このページでは、それらの中から『真空成形』と『圧空成形』について紹介します。
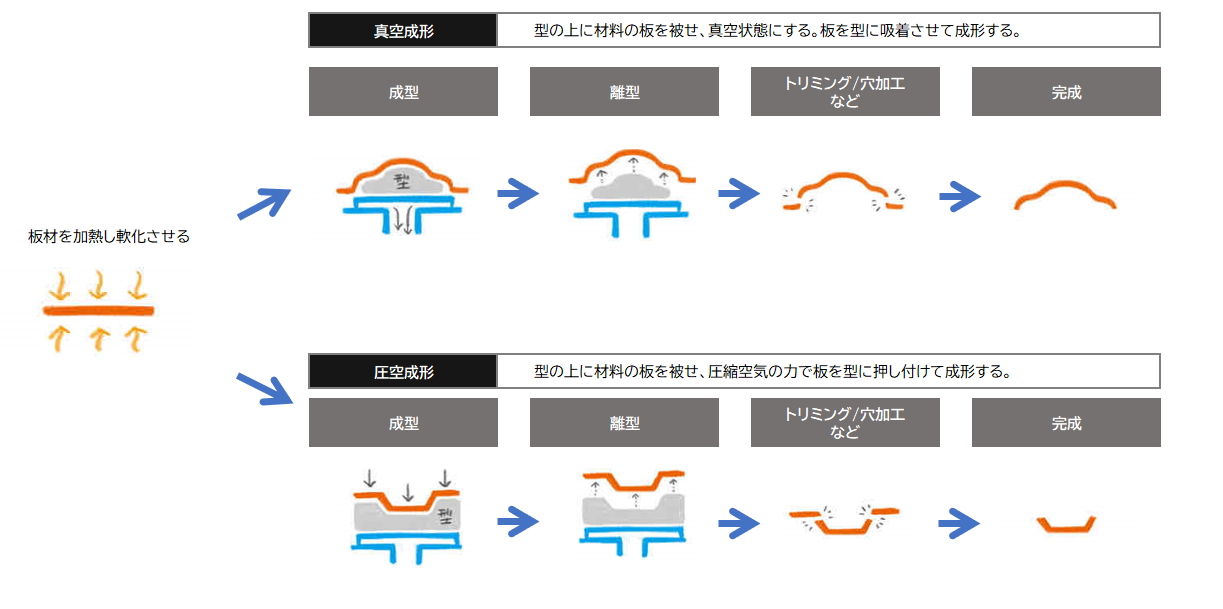
◆真空成形
加熱して軟化したシートと型との空間を真空状態(型に開けた微小な穴から空気を抜き真空にする)にする事で、シートを型に密着させて変形させ、目的の形状にする成形方法です。
型の材料としては、一般的に金属(アルミなど)を用いることが多いですが、試作の場合は樹脂製や木製の型を用いる場合もあります。
樹脂製や木製の型は、金属型と比べると低いコストや短い期間で製作できるメリットがありますが、加熱したシートの熱によって型自体が変形してしまう状況が発生し、連続して成型すると製品寸法が徐々に変わってしまうというデメリットがあります。
形状についての注意点としては、コーナー部分が真空の力で肉薄になりやすく、型に当たっていない面は寸法にバラつきが出るという点が挙げられます。
また、厚みのあるシートを使用する場合や、深い形状に成形する場合には、シートにシワが寄ることで綺麗に成形できないこともあります。
成型加工後に型から外せるように、型には勾配を付けなければならないといった、技術的な注意点もあるため、設計段階で加工メーカーと入念な打ち合わせを行うことも重要になります。
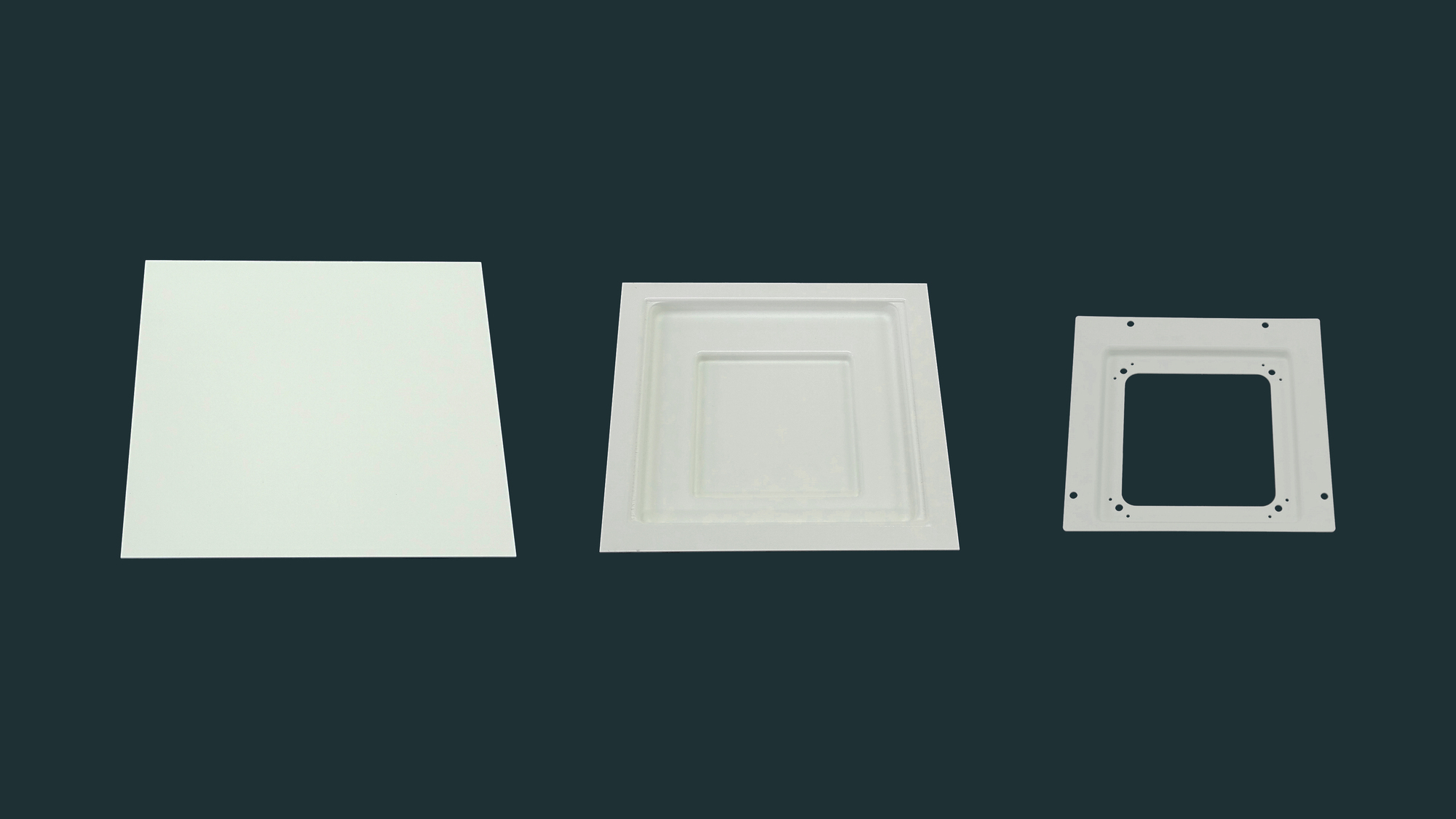
◆圧空成形
加熱して軟化したシートを圧縮空気で型に密着させ、型の形状を写し取る成形方法です。
真空成形と並んで広く利用されている加工方法です。
真空成形では大気圧以上の圧力をかけることはできませんが、圧空成形では圧縮した空気で押し付ける方法のため、より高い圧力を掛けることができることで、肉厚のバランスが取れた、より精度の高い加工が可能になります。
真空成形の場合は、基本的に製品裏側に型が当たるため、外形寸法にバラつきが出ますが、圧空成形では製品表面に型が当たることで、外形寸法が安定して得られ、表面形状もシャープに仕上がります。
また、真空成型では対応できないアンダーカット形状にも対応できるといったメリットもあります。